|
联 系 方 式 |
电 话: |
0371-66559606 |
手 机: |
13838271516 |
|
|
PAC产品系列 |
|
|
 |
茂名石化公司炼油厂双塔汽提(加压脱硫化氢、回收液氨)实例
- 1982年茂名石化公司炼油厂建成一套酸性水单、双塔汽提装置,该装置是加氢裂化装置的配套工程。单塔处理催化裂化、焦化装置较低浓度的酸性水,双塔处理加氢裂化、重整和加氢精制装置产生的高浓度酸性水。
- 工艺流程简述
催化裂化、焦化装置来的酸性水经泵分为两股,一股作为冷进料,进入单塔顶部填料层上;一股换热至140℃,作为热进料进入单塔上部第1层塔板。塔顶酸性气经分液后送至硫黄回收。含氨水汽从第19层侧线抽出,送入双塔部分的氨汽提塔。单塔塔底净化水送至污水处理场。
重整、加氢精制装置酸性水经低浓度进料泵输送;加氢裂化装置酸性水经高浓度进料泵输送。重整、加氢精制酸性水一股作为冷进料进入硫化氢塔顶填料层上,另一股与加氢裂化酸性水在泵出口汇合后,经换热至140℃,作为热进料,进入硫化氢塔上部第7层塔板。塔底用重沸器供热。汽提出的酸性气自塔顶经分液罐后,酸性气送至硫黄回收。硫化氢塔底循环液与进料酸性水换热后,温度降至138℃,自压进入氮塔第11层塔板,作为热进料。单塔侧线抽出的含氨水汽,进入氨塔的第23层塔板,作为气相热进料。氨塔底用重沸器供热。汽提出的气氨自塔顶经冷凝冷却后,进入分液罐进行气液分离,自罐顶分出的气氨进入氨精制系统生产液氨。分出的冷凝液约1/4进入硫化氢塔第1层塔板,作为硫化氢塔冷进料。另外3/4打入双塔的氨塔塔顶作为氨塔回流。氨塔塔底净化水送至污水处理场。详见图2-36。
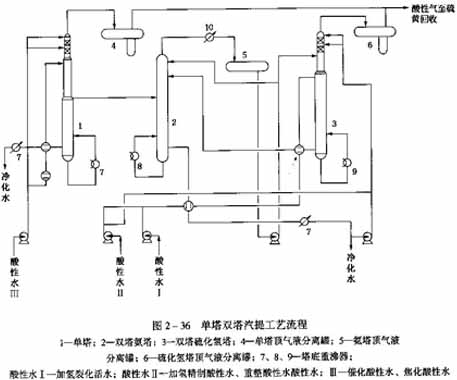
- 原料及产品组成
原料及产品组成见下表。
原料及产品组成
项目 |
原设计组成 |
1987年实际生产组成 |
1988年实际生产组成 |
H2S |
NH3 |
H2S |
NH3 |
H2S |
NH3 |
单塔进料酸性水/(mg/L) |
|
|
1409 |
1712 |
4094 |
4663 |
其中催化裂化水/(mg/L) |
836.8
|
793.57 |
|
|
|
|
焦化水/(mg/L) |
6606.80 |
2930.54 |
|
|
|
|
双塔冷进料水/(mg/L) |
|
|
2323 |
2676 |
5066 |
8325 |
其中重整水/(mg/L) |
8583.09 |
3411.03 |
|
|
|
|
加氢精制水/(mg/L) |
8583.09 |
3411.03 |
|
|
|
|
双塔热进料水/(mg/L) |
64300 |
32200 |
26198 |
49581 |
41576 |
64613 |
其中加氢裂化水/(mg/L) |
单塔净化水/(mg/L) |
<100 |
<300 |
17 |
40 |
31 |
60 |
双塔净化水/(mg/L) |
<100 |
<300 |
14 |
28 |
24 |
43 |
单塔酸性气/%(体) |
97.4 |
<1 |
48.14 |
0.65 |
47.33 |
0.75 |
双塔酸性气/%(体) |
97.4 |
<1 |
78.70 |
0.83 |
86.87 |
0.93 |
双塔气氨 |
微量 |
|
8.08mg/m3 |
99.59% |
3.57mg/m3 |
99.68% |
- 物料平衡
原料水量及产品产量分别见一下两表。
原料水量
项目 |
酸性水I |
酸性水II |
酸性水III |
总计 |
催化水 |
焦化水 |
重整水 |
加氢精制水 |
加氢裂化水 |
水量/(t/h) |
6 |
5 |
3 |
8 |
6.847 |
28.847 |
水量/(t/a) |
48000 |
40000 |
24000 |
64000 |
54776 |
230776 |
产品产量
项目 |
单塔系统 |
双塔系统 |
总计 |
kg/h |
t/a |
kg/h |
t/a |
kg/h |
t/a |
净化水 |
10000 |
80000 |
17992.7 |
143941.6 |
27992.7 |
223941.6 |
硫化氢 |
35.83 |
286.64 |
546 |
4368 |
581.83 |
4654.64 |
液氨 |
|
|
263 |
2104 |
263 |
2104 |
1987年单塔生产346天,双塔生产355天,共处理酸性水260kt,平均处理量为30.97t/h,为设计能力的107.29%,其中单塔11.24t/h,双塔19.74t/h,分别为设计能力的102.2%和110.6%。生产液氨1.42kt,平均日产4.72t。净化水含硫化氢合格率100%,含氨合格率95.74%。液氨含硫化氢8.08mg/m3。
- 主要工艺设备
单塔汽提硫化氢塔:¢600/¢800/¢1000*37718*20*16、12、*(10+2)矩鞍型填料两层(¢600),浮阀塔板40层(¢800段16层、¢1000段24层),板间距450mm。
双塔汽提硫化氢塔:¢800/¢1000*31502*16*(10+2),矩鞍型填料两层(¢800段),浮阀塔板30层(¢800段6层、¢1000段24层),板间距450mm。
双塔汽提氨塔:¢1400*29252*16、(10+2),浮阀塔板30层,板间距450mm。
单塔硫化氢塔顶气液分离罐:¢800*2504*10卧式
双塔硫化氢塔顶气液分离罐:¢800*2504*10卧式
氨液分离罐:¢1400*5800*10卧式
单塔硫化氢塔底重沸器:GCH-1001-16/10-120 B=600
双塔硫化氢塔底重沸器:GCH-1001-16/10-120 B=600
双塔氨塔底重沸器:GCH-1200-16/10-170 B=600
- 主要工艺操作条件
(1)单塔汽提硫化氢塔
塔顶温度:45℃;冷进料温度:409;热进料:130℃;侧线抽出温度:158℃;塔底温度:160℃;塔顶压力:0.5MPa
(2)双塔汽提硫化氢塔
塔顶温度:45℃;冷进料温度:40℃;热进料:134℃;塔底温度:164℃;塔顶压力:0.55MPa
(3)双塔汽提氨塔
塔顶温度:115℃;冷进料温度:40℃;热进料:134℃;塔底温度:141℃;塔顶压力:0.24MPa
(4)单塔顶气液分离罐
温度:45℃;压力:0.5MPa
(5)硫化氢塔顶气液分离罐
温度:45℃;压力:0.55MPa
(6)双塔氨液分离罐
温度:38℃;压力:0.2MPa
- 消耗指标及能耗
下表中消耗指标及能耗是包括全装置即单双塔汽提、液氨精制及公用工程的设计数据。
消耗指标及能耗
序号 |
项目 |
单位耗量 |
小时耗量 |
能耗指标 |
单位能耗/(MJ/t) |
总能耗/(MJ/h) |
单位 |
数量 |
单位 |
数量 |
单位 |
数量 |
1 |
循环水 |
t/t |
14.27 |
t/h |
411.6 |
MJ/t |
4.19 |
59.8 |
1724.6 |
2 |
电力 |
kW·h/t |
3.85 |
kW |
111 |
MJ/kW·h |
12.56 |
48.3 |
1394.2 |
3 |
净化空气 |
m3/t |
4.16 |
m3/h |
120 |
MJ/m3 |
1.67 |
6.9 |
200.4 |
4 |
1MPa蒸汽 |
t/t |
0.285 |
t/h |
8.212 |
MJ/t |
3181.9 |
906.8 |
26129.8 |
|
总计 |
|
|
|
|
|
|
1021.8 |
29449 |
蒸汽用量是决定装置能耗的主要因素,根据现场各塔底重沸器实耗最大蒸汽量计算的能耗数值比设计值低。设计单塔汽提重沸器2.072t/h,硫化氢塔底重沸器1.952t/h,氨塔底重沸器3.688t/h,合计蒸汽耗量7.712t/h,总能耗为24539.4MJ/h,单位能耗856.6MJ/t酸性水。生产实耗各塔底重沸器蒸汽耗量最大值:单塔汽提重沸器0.16t/t酸性水、硫化氢塔底重沸器0.1t/t酸性水、氨塔底重沸器0.16t/t酸性水、按各塔进料量折合蒸汽耗量,单塔汽提重沸器1.76t/h,硫化氢塔底重沸器1.78t/h,氨塔底重沸器2.86t/h、各塔蒸汽耗量合计6.4t/h,总能耗为20364.6MJ/h,单位能耗706MJ/t酸性水。
- 装置设计及生产特点
经多年生产实践,并从上述数据可概括该装置具有以下特点:
装置操作具有一定弹性,生产中原料水量、水质经常变化,尤其水中污染物含量远远超过设计值,装置均能保证正常生产。
处理效果好,净化水合格率高。由于设计中采用变径的汽提塔,并选用合理的水力参数,为获得较好的汽提效果创造了条件。生产中不断总结经验,提高操作水平,例如掌握好提供合乎要求的汽提热源;控制好汽提塔各关键点温度;注意提高硫化氢塔的拔出率;注意稳定氨塔顶回流罐的压力等操作要点。
单塔侧线抽出直接进入双塔的氨汽提塔,与双塔汽提的气氨一并处理,回收了高纯度液氨。该流程充分利用装置内双塔汽提的有利条件,取消分凝冷凝设备,避免在单塔中形成高浓度内循环,节约单塔汽提蒸汽用量。另外侧线抽出以气相进入氨塔,可减少双塔汽提蒸汽用量,这也是与同类装置相比,双塔在处理高浓度酸性水的情况下,尚能节约蒸汽用量的原因之一。
采用反馈控制,使操作稳定,便于调节。双塔汽提操作控制的核心设备是氨塔顶回流罐。该回流罐存在着氨-硫化氢-二氧化碳-水多元体系的相平衡。故选择合适的气-液平衡条件,保持其压力稳定,是全装置平稳操作的关键,是保证气氨产品质量的重要因素之一。该设计采用反馈自动控制--即从氨压机系统向回流罐引入气氨,以维持其压力的稳定。在生产中不管是原料水质、水量的变化,或其他外界因素的干扰,在严重破坏系统相平衡的情况下,回流罐的压力仍能稳定在0.2MPa,装置仍能保持稳定操作。故采用反馈控制,是
加强抗干扰能力,保证全装置平稳操作的重要手段。
国内首次采用以浓氨水循环洗涤气氨的精制流程,以获得高纯度液氨,取得了较满意的效果。
- 巩义市泰和水处理材料有限公司专业生产聚合氯化铝、聚合氯化铝铁、碱式氯化铝、硫酸铝、硫酸亚铁、聚合氯化铝铁、三氯化铁、硫酸铁、各种无机盐类絮凝剂、无机铁盐、铝盐、助凝剂聚丙烯酰胺等净水药剂的专业厂家。
|
|
|